پوشش آلومينايدي و سایر پوشش ها در توربینهای گازی
استفاده پوشش آلومينايدي در دماي بالا روي سطح سوپر آلياژ عبارت است از یکلایه سطحي از ماده سراميكي يا فلزي يا تركيبي از اين دو كه قادر به جلوگيري يا كاهش واكنش مستقيم بين زمينه و محيط مخرب اطراف باشد. اين تخريب ممكن است كاهش ضخامت فلز در اثر اكسيداسيون و خوردگي يا كاهش خواص مكانيكي زمينه به علت ديفوزيون اجزا مخرب به داخل آلياژ در دماي بالا باشد.
گرچه پوششهای مورداستفاده در قطعات قسمت داغ توربين با توجه به مقاومت به اكسيداسيون و خوردگي آنها طراحي میشوند، ولي با توجه به شرايط كاري و اقتصادي، اين پوششها بايد داراي خصوصيات زير باشند :
خصوصیات پوشش های آلومینایدی
– مقاومت كافي در برابر اكسيداسيون، خوردگي داغ و در برخي موارد سايش
– پيوند مستحكم با زمينه
– مقاومت كافي در برابر تنشهای حرارتي و مكانيكي
– پايداري ديفوزيوني
– قابليت انعطاف كافي
– عدم تأثیر مخرب بر خواص آلياژ زمينه
– ضخامت كم و يكنواخت
– عدم تخريب موضعي و دارا بودن كيفيت سطحي مطلوب ازنظر آئرودینامیکی
– عملي بودن فرايند و اقتصادی بودن
بر اساس خصوصيات فوق، امروزه سه سيستم پوششي اصلي در توربینهای گاز بكار میرود كه عبارتاند از :
- پوششهای نفوذی
- پوششهای روكشي
- سیستمهای سد حرارتي
الف- پوششهای نفوذي
اين پوششها كه عموماً از جنس فلزي (بين فلزي) هستند، بر سه نوع آلومينايدي، كرومايدي، سيلسايدي میباشند. اين پوششها با روشهای مختلفي از قبيل سمانتاسیون پودری، دوغابیو رسوب بخار شيميايي اعمال میگردند كه متداولترین آنها ، میباشد كه تشكيل آنها اساساً توسط مكانيزم نفوذ كنترل میشود و به همين علت كه ايجاد آنها بستگي به نفوذ متقابل ميان پوشش آلومينايدي و فلز پايه دارد، اين پوششها تا حدي از خواص مكانيكي آلياژ پايه میکاهند.
ب- پوششهاي روكشي
اين پوششها شامل آلياژهاي بر پايه سيستم (M:Co,Ni Co,Co –Ni) M-CrAlX و (عناصر افزودني فعال مثل X :Hf,Ta,Si,Y) میباشد.
علت اضافه كردن عناصر فعال افزايش چسبندگي لايه اكسيدي و كاهش تخریبهای سطحی پوشش میباشد. اعمال اين سيستمها اغلب بهوسیله روش پلاسما اسپري يا PVD انجام میگیرد مزيت پوششهاي روكشي نسبت به نفوذی اين است كه خواص مكانيكي فلز پايه را كمتر تضعيف میکنند.
ج- پوششهای سد حرارتي
این پوششها شامل لايه سراميكي با هدايت حرارتي پایینبر روي لايه روكش M-CrAlX موجود روي سطح فلز میباشدپوششهاي TBC به علت داشتن خواصي چون نقطه ذوب بالا، ظرفيت حرارتي كم، انعكاس شعلهای مناسب، انبساط حرارتي مشابه نسبت به فلز پايه و مقاومت در برابر سايش و اكسيداسيون بهطور گستردهای در توربینهای گازي مدرن مورداستفاده قرارگرفته است.در این پوششها جهت جلوگيري از ترك خوردن لایهای ترد سراميكي ذرات پایدارکنندهای چونY2O3,CeO2,MgO ، به پوشش افزوده میشود. پوششهاي سد حرارتي معمولاً توسط روش اسپري پلاسمايي يا روش PVD ايجاد میگردند.
پوشش آلومینایدی نفوذی
پوشش آلومينايدي نفوذي كه به پوششهاي آلومينايدي شهرت دارند، در اوایل دهه 1960 ابداع شدند. اولين استفاده پوششهای آلومينايدي در پرههای ايرفويل توربینهای هوايي بوده است از آن زمان تاكنون، اين پوششها در مسير تحول خود تغييرات زيادي را هم در فرآيند و هم در تركيب شيميايي داشتهاند بهطوریکه امروزه درنتیجه اين تغييرات، پوششهاي تجاري متعددي براي استفاده در كاربردهاي مختلف ایجادشده است(جدول 2-1). پوششهاي آلومينايدي بر روي سوپر آلياژهاي پايه نيكل يا پايه كبالت، با تشكيل تركيبات بين فلزي نظير يا توسط فرايند نفوذي ايجاد میشوند. خواص حفاظتي اين پوششها بر مبناي طبيعت پوستههای اكسيدي Al2O3 قرار دارد كه در دماي كاري بر روي آنها تشكيل میشوند.
جدول2- 1: پوشش آلومينايدي تجاری
نام پوشش | تولید کننده | ترکیب شیمیایی | روش تولید |
PWA 73 | Pratt&Whitny | آلومیناید | فرآیند محفظه ای با اکتیویته بالا |
PWA 273 | Pratt&Whitny | آلومیناید | فرآیند محفظه ای با اکتیویته پایین |
PWA 275 | Pratt&Whitny | آلومیناید | فرآیند بالامحفظه ای با اکتیویته پایین |
MDC 200 | Howmet | آلومیناید | فرآیند محفظه ای با اکتیویته پایین |
MDC 210 | Howmet | آلومیناید | فرآیند محفظه ای با اکتیویته بالا |
RT 21 | Chromalloy | آلومیناید | فرآیند محفظه ای با اکتیویته بالا |
CODEP | General Electric | آلومیناید | فرآیند محفظه ای با اکتیویته بالا |
ALPAK | Rolls Royce | آلومیناید | فرآیند محفظه ای با اکتیویته بالا |
Serma Tel W | Sermatech | دوغاب آلومیناید | فرآیند محفظه ای با اکتیویته بالا |
روشهای اعمال
مورفولوژي پوشش آلومينايدي وابسته به اكتيويته آلومينيوم در تركيب جعبه سمنتاسيون و سيكل عمليات حرارتي اعمالي بر آن است. به همين علت با توجه به اینکه پوشش براثر نفوذ آلومينيوم به درون سطح يا نفوذ نيكل به سمت بيرون سطح صورت پذيرد لایههای مختلفي تشكيل میگردند كه میتوان آنها را در دو گروه تقسیمبندی نمود:
الف- ايجاد لايه آلومينايدي (NiAl) در يك سيكل عمليات حرارتي كه در اين شرايط، نفوذ غالب نيكل بهطرف خارج سطح امکانپذیر میشود. دماي پوشش دادن در اين گروه بين ℃1000 تا ℃1100 میباشد.
ب- ايجاد لايه آلومينايدي با تركيب Ni2Al3 و سپس تغيير آن به لايه NiAl توسط عمليات نفوذ آنيل در اين فرآيند در سيكل اول نفوذ آلومينيوم بهطرف داخل سطح انجامگرفته و در مرحله بعدي نفوذ نيكل به سمت خارج صورت میپذیرد. سيكل عمليات حرارتي دومرحلهای است و محدوده دمايي مرحله نخست بين 700 تا 950 درجه سانتیگراد و مرحله بعد كه نفوذ آنيلينگ است در محدوده دماي 1000 تا 1100 درجه سانتیگراد میباشد.
همانطور كه شكل 2-7 نشان میدهد اين دو نوع فرايند، دو نوع مورفولوژی مختلف پوشش را به وجود میآورند.
شکل2- 7: ) الف) مورفولوژی پوشش آلومينايدي اكتيويته بالا و (ب) مورفولوژي پوشش آلومينايدي اكتيويته پايين.
ترکیب فازی پوشش آلومينايدي
مطالعات زیادی روی ترمودینامیک، سینیتیک، ساختار و مکانیزمهای تشکیل پوشش آلومينايدي صورت گرفته است. همچنين مشاهده شده كه رشد لايه آلومينايدي از قانون پارابوليكي پيروي مي كند. تشكيل پوشش آلومينايدي با نفوذ آلومينيوم به داخل آلياژ پايه نيكل و تشكيل تركيبات بين فلزي نيكل- آلومينيوم صورت مي گيرد. بنابراين آشنايي با دياگرام فازي تعادلي دوتايي نيكل – آلومينيوم در درجه حرارتهاي آلومينايزينگ براي فهم خصوصيات ريز ساختاري ايجاد شده در پوششهاي آلومينايدي ضروري است. زيرا لايه بين فلزي تشكيل شده روي آلياژهاي پايه نيكل از فازهاي موجود در اين دياگرام دوتايي تشكيل شده است.
دياگرام فازي NiAl در شكل 2-8 آورده شده است. دراين دياگرام پنج تركيب بين فلزي وجود دارد كه مشخصات آنها در جدول 2-2 ارائه شده است. تركيب NiAl با نقطه ذوب ℃1638 ديرگدازترين و تركيب نيمه پايدار Ni5Al3 با نقطه ذوب ℃700 زود ذوب ترين تركيب هاي بين فلزي در اين دياگرام هستند. همان طور كه در شكل 2-8 ديده مي شود، فازهاي موجود در اين دياگرام در درجه حرارتهاي آلومينايزينگ ، فازهاي بين فلزي Ni2Al3،NiAl،Ni3Al هستند. اگرچه امكان وجود تمام اين فازها در پوشش آلومينايدي بر روي آلياژهاي پايه نيكل وجود دارد ولي NiAl و Ni2Al3 تنها فازهايي هستند كه معمولاً به عنوان فازهاي موجود دراين پوشش گزارش شدهاند. Ni2Al3 داراي ساختار هگزاگونال باپارامترهاي شبكه و است. اين فاز تا اندازه اي ترد بوده و نقطه ذوب نسبتاً پاييني دارد كه به صورت پريتكتيك در ℃1133 تشكيل ميشود و در محدوده 37 تا 42 درصد اتمي نيكل به صورت يك فاز همگن وجود دارداز طرف ديگر، NiAl فاز پايدارتري نسبت به Ni2Al3 است و با محدوده فاز گسترده خود پوشش محافظ مناسبي براي سوپرآلياژهاي پايه نيكل است و به اين علت، مهمترين فاز در پوششهاي آلومينايدي روي سوپرآلياژهاي پايه نيكل محسوب مي شود. NiAl داراي شبكه مكعبي از نوع CsCl (B2) با ثابت شبكه است كه در ℃1638 ذوب مي شود و محدوده پايداري آن در ℃1000 در محدوده 42 تا 65 درصد اتمي نيكل قرار دارد.
جدول2- 2: تركيبات بين فلزي در سيستم NiAl
space group | personal symbol | composition wt%Ni | Phase |
Fm3m | cF4 | 0 to 0.24 | (Al) |
Pnma | oP16 | 42 | Al₃Ni |
P3m1 | hP5 | 55.0 to 60.7 | Al₃Ni₂ |
Pm3m | cP2 | 61 to 83.0 | AlNi |
Cmmm | . . . | 79 ͠ 82 | Al₃Ni₅ |
Pmvm | cP4 | 85 to 87 | AlNi₃ |
Fm3m | cF4 | 89.0 to 100 | (Ni) |
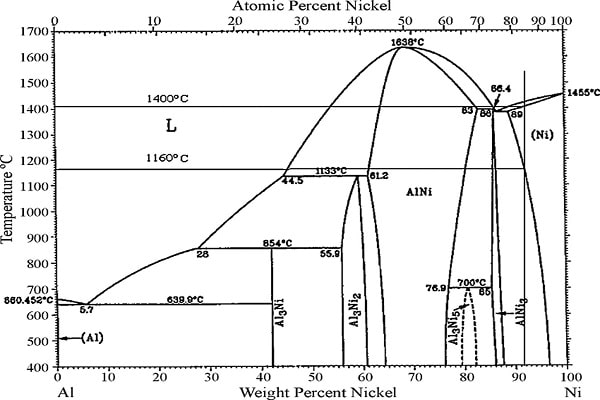
شکل2- 8: دياگرام فازي سيستم دوتایي نيكل – آلومينيم
به علت نقش مهم نفوذ در تشكيل پوشش آلومينايدي ، تحقيقاتي روي نفوذ آلومينيم و نيكل در آلياژها و تركيبات بين فلزي مختلف در سيستم دوتايي NiAl صورت گرفته است. مطالعات اوليه توسط جانسون[6] و ریک[7]]33[ نشان داد كه تنها اتمهاي آلومينيم در آلومينايدهاي غني از آلومينيم قادر به حركت بوده و اتمهاي نيكل فقط مي توانند در آلومينايدهاي فقير ازآلومينيم تحرك داشته باشند. بنابراين پوشش هاي با اكتيويته بالاي آلومينيم در شروع به سمت داخل رشد كرده در حاليكه پوشش هاي با اكتيويته پايين به سمت خارج به رشد و نمو خود ادامه مي دهند ولي تاثير تركيب NiAl دراين مطالعات مورد توجه قرار نگرفته است.
مکانیزم های تشکیل پوشش
گووارد دو نوع اصلي پوشش آلومينايدي را روي سوپر آلياژهاي پايه نيكل شناسايي كرده است. اختلاف اساسي اين دو نوع پوشش در مكانيزم تشكيل آنهاست كه به نوبه خود به درجه حرارت آلومينايزنيگ و فعاليت آلومينيم در داخل محفظه پوشش دهي بستگي دارد و برحسب جهت نفوذ عناصر نيكل و آلومينيم در موقع تشكيل آنها، به پوششهاي نفوذ داخلي و نفوذ خارجي شهرت دارند.
مكانيزم تشكيل پوشش با فرآیند HALT
در مرحله نخست فرايند آلومينايزنيگ با اكتيويته بالاي آلومينيم در لايه خارجي پوشش، فاز Ni2Al3 به همراه يكسري فازهاي رسوبي ايجاد میشوند (شكل 2-9). در این پوشش کاربیدهای موجود در زمینه سوپرآلياژ نيز پس از عمليات پوشش دادن در این لايه مشاهده میگردند كه اين كاربيدها میتوانند بهعنوان علائمي جهت درك نفوذ غالب نيكل يا آلومينيم در رشد پوشش مورد استفاده قرار گيرند. توزيع يكنواخت عناصر آلياژي همچون كروم و موليبدن بسته مقدار حلاليتشان، در اين لايه مشهود است. رشد اين لايه تا زماني ادامه مییابد كه گراديان آلومينيم در سطح لايه خارجي وجود داشته باشد. مرحله بعدي تبديل لايه غني از آلومینیم به لايه غني از نيكل میباشد كه در اثر نفوذ بهطرف خارج نيكل در فاز (NiAl)β و نفوذ آلومينيم در فاز (NiAl)β غني از آلومينيم ميسر میگردد. در لایه بيروني پوشش رسوباتي به وجود میآیند كه اين رسوبات در مرحله نخست عمليات آلومينايزنيگ نيز وجود داشتهاند و اين رسوبات در اين شرايط پايدار میشوند. از فازهاي مهم در اين ناحيه فازهاي α-CrMo و همچنين كاربيدهاي نوع MC را میتوان نام برد. در مرحله آخر فرايند، نفوذ غالب نيكل در فاز β حاصل میشود و باعث افزايش ضخامت میشود.
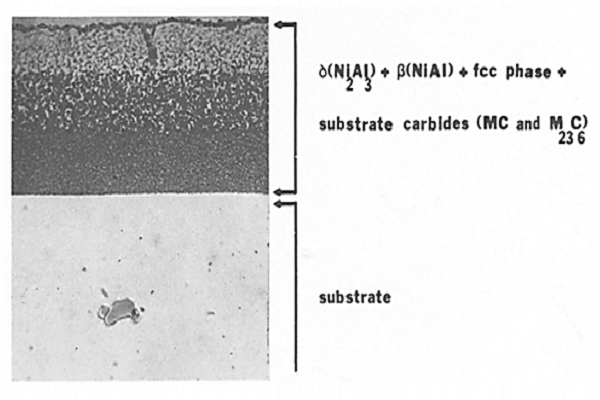
شکل2- 9: مرحله نخست عمليات آلومينايزينگ بر روي سوپرآلیاژ Udmit 700 را نشان میدهد
در سوپرآلياژهاي پايه نيكل در نزديكي فصل مشترك بين پوشش و زمينه به علت خالي شدن نيكل ونفوذ ان به سمت سطح و ترکیب با آلومینیم باعث ايجاد یکلایه فازي بهصورت NiAl میشود. اين لايه (ناحيه 3 شكل 2-10) حاوي تعداد زيادي از فازهاي رسوبکرده میباشد. به علت عدم حلاليت عناصر آلياژي در فاز β در اين ناحيه كاربيدهایي به فرم M23C6(CrxMoyC6), MC(TiC) تشكيل میگردند كه اين كاربيدها بيشتر در اثر واكنش تيتانيم، كروم، موليبدن با كربن زمينه به وجود میآیند. اگر مقدار كربن در سوپر آلیاژ به اندازه كافي نباشد اين واکنشها انجام نگرفته و تنها فازهاي لایهای شكل و غني از كروم و موليبدن بنام سيگما در فاز زمينه به وجود خواهد آمد. يكي از دلايل ديگر جهت اثبات مكانيزم اشاره شده، اين است كه اگر در تركيب سوپرآلياژ عنصر آلومينيم وجود نداشته باشد اين لايه تشكيل نمیگردد. اين موضوع توسط آلومينايزينگ آلياژ پايه نيكل Hastalloy به اثبات رسيده است. ضخامت لايهβ غني از نيكل (ناحيه دو شكل 2-10) بانفوذ بيشتر نيكل از سوپر آلياژ به بيرون زيادتر میشود و رشد اين لايه منوط به كاهش نيكل زمينه سوپرآلياژ و آلومينيوم در ناحيه خارجي پوشش میباشد.
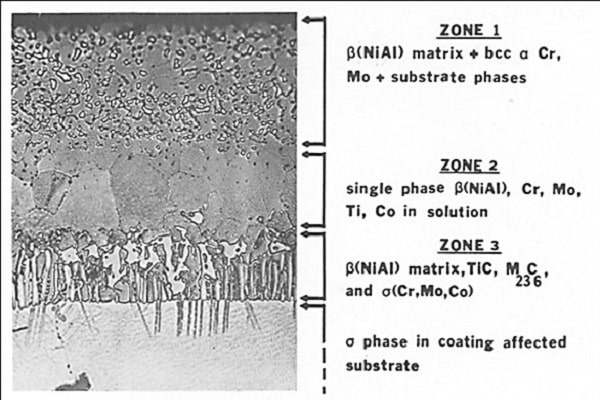
شکل2- 10: میکرو ریزساختار پوشش آلومينايزينگ در شرايط اكتيويته بالاي آلومينيم را بر روي سوپر آلياژ Udmit 700 نشان میدهد. عمليات نفوذ آنيلينگ دردماي 1675 درجه فارنهايت و به مدت 4 ساعت انجامشده است.
تركيب و ساختار فازهاي در فاز زمينه در ناحيه نفوذي پوشش، در يك آلياژ نسبت به آلياژ ديگر متفاوت است. طبق تحقيقات، مشخصشده است كه نسبت كاربيدهاي M6C به فاز در سوپرآلیاژ MAR-M200 بيشتر میباشد. در سوپرآلياژ IN100 فازهاي كاربيدي بهصورت TiC و مشاهده شدهاند. در اين ناحيه ضخامت لايه نفوذي وابسته به دما بوده و با افزايش دما ضخامت لايه زيادي میگردد. دامنه پايداري فاز بين 1400 تا 1800 درجه سانتیگراد میباشد.
مكانيزم تشكيل پوشش با فرآیندLAHT
ناحيه خارجي اين پوشش (ناحيه 1 شكل 2-11) حاوي فاز NiAl-β با تركيب متغير استوكيومتري است. درصد آلومينيم در سطح نسبت به لایههای زيرين بيشتر است. فاز β در سطح خارجي تك فاز بوده و حاوي عناصر آلياژي بهصورت محلول جامد میباشد. كاربيدهاي MC كه در آلياژ پايه وجود داشتهاند نيز در پوشش يافت میشود. اين كاربيدها بيشتر در فصل مشترك نواحي يك و دو قرار میگیرند. در اين فرايند نيز همانند پوششهاي آلومينايدي با اكتيويته بالاي آلومينيوم ناحيه نفوذ وجود دارد (ناحيه 2 شكل 2-11).
مقايسه ناحيه نفوذ در فرآيندهاي اكتيويته بالا و پائين در شرايط يكسان نشان میدهد كه ناحيه نفوذ در فرايند اكتيويته پائين آلومينيم بزرگتر از ناحيه نفوذ در فرايند اكتيويته بالاي آلومينيم میباشد. علت اين امر میتواند ناشي از خروج غالب نيكل در فرايند اكتيويته پايين آلومينيم باشد.
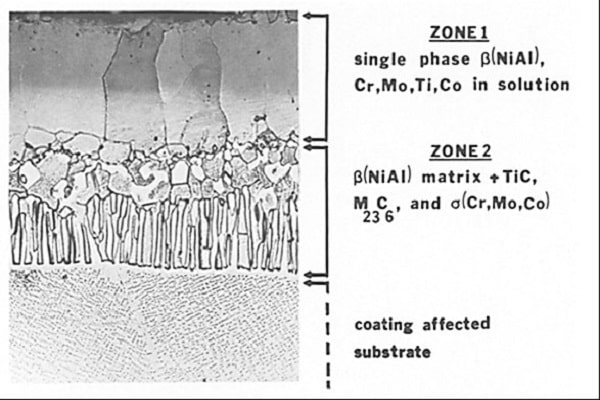
شکل2- 11: میکرو ساختار و فازهاي مشخصه در فرايند آلومينايزينگ با اكتيويته پايين آلومينيم بر روي سوپر آلیاژ Udmit 700 را نشان میدهد.
پوشش آلومينايدي اصلاح شده با سیلیسیم
حضور سیلیسیم به جای بخشی از آلومینیم در مواد اولیه پوشش دهی آلومینایزینگ منجر به تشکیل لایه آلومیناید حاوی سیلیسیم و ترکیبات سیلیسیم دار معروف به پوشش آلومیناید اصلاح شده با سیلیسیم (یا به عبارت دیگر پوشش AlSi) می شود. برای اعمال این گونه پوشش ها از دو روش سمانتاسیون پودری و دوغابی استفاده می شود. اما اصلاح با روش سمانتاسیون پودری به واسطه اختلاف زیاد فشار بخار هالیدهای آلومینیم و سیلیسیم مشکل است. بنابراین از روش دوغابی به عنوان یک فرآیند جایگیزین برای روش سمانتاسیون پودری استفاده می شود. معروف ترین کاربرد روش دوغابی اعمال پوشش سرمالوی جی است. سیلیسیم تاثیر بسیار مناسب بر مقاومت در برابر اکسیداسیون سیکلی و خوردگی داغ نوع دوم دارد. سیلیکونایزینگ می تواند به صورت پودری انجام شود که در این روش سیلیسیم به صورت فلزی، NH4Cl به عنوان فعال کننده و Al2O3 به عنوان پرکننده استفاده می شود. همچنین می توان سیلیکونایزینگ را به صورت مرحله ای مجزا قبل یا بعد از آلومینایزینگ انجام داد. از مشکلات این روش می توان به تردی لایه سیلیسیم و همچنین پایین بودن دمای ذوب ترکیب یوتکتیک آن اشاره کرد.
ک . شیروانی در یک پژوهش با بررسی رفتار خوردگی داغ پوشش های اصلاح شده با سیلیسیم، حداقل مقدار سیلیسیم برای ایجاد مقاومت به خوردگی پوشش های نفوذی را 10- 12 درصد وزنی گزارش کرده است.
همانطور که قبلا اشاره شد، پوشش های اصلاح شده با سیلیسیم ( شکل 2-12) مقاومت بسیار خوبی نسبت به اکسیداسیون سیکلی و خوردگی داغ از خود نشان می دهند. البته این مقاومت بستگی زیادی به زیرلایه نیز دارد. به طور مثال پوشش AlSi بر روی سوپرآلیاژ B-1900 عمر بیشتری را نسب به همین پوشش بر روی سوپرآلیاژ VIA نشان داده است. این اثر به نوع اکسیدهایی که باتوجه به عناصر موجود در هر آلیاژ ممکن است در پوسته اکسید سطحی تشکیل شود، نسبت داده شده است. برخی آزمایشها نشان میدهد که پوشش AlSi برروی زیر لایه مشابه حداقل تا 4 برابر پوششهای آلومیناید ساده مقاومت از خود نشان میدهد. همچنین مقاومت به خوردگی داغ این پوششها به حلالیت بسیار پایین اکسید سیلیسیم در دامنه وسیعی از اسید نمک مذاب دارد. به طور کلی مقاومت خوب این پوششها در برابر خوردگی داغ دمای بالا را میتوان به عوامل ذیل نسبت داد:
الف: جایگزینی اکسید مقاومتر SiO2 به جای بخشی از Al2O3 آسیب پذیر در پوسته اکسیدی.
ب : تمایل به تشکیل فازهای پایدار سیلیسایدی با عناصر دیرگداز نظیر مولیبدن، تیتانیوم تنگستن در نتیجه کاهش میزان جدایش این عناصر در لایه اکسید محافظ سطحی.
ج: سیلیسیم برخلاف آلومینیم قادر به تشکیل سولفید نبوده و مقاوم به نفوذ گوگرد است. از عیوب این پوشش آلومينايدي می توان به حساسیت به ترک نام برد. علیرغم بالا بودن حد بحرانی جوانهزنی ترک، رشد ترک پس از شروع سریع است. اگرچه این ترکها به دلیل عدم نفوذ به زیرلایه موجب شرایط بحرانی نمیشوند، اما در نهایت مسیرهای خوردگی را به زیرلایه باز مینمایند.
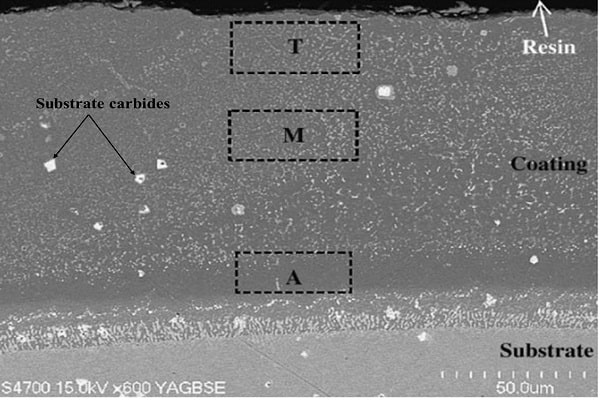
شکل2- 12:تصویر سطح مقطع پوشش سیلیسیم آلومیناید دوغابی
جدول2- 3: پوششهای نفوذی تجاری اصلاح شده با سیلیسیم
نام پوشش | تولید کننده | ترکیب شیمیایی | روش تولید |
Jo Coat | Pratt&Whitny | دوغاب آلومیناید+ Si | فرآیند محفظه ای با اکتیویته بالا |
Serma Loy J | Sermatech | دوغاب آلومیناید + Si | فرآیند محفظه ای با اکتیویته بالا |
Elcoat 360 | Elbar | دوغاب Ti+ Si | فرآیند محفظه ای با اکتیویته بالا |
اصلاح پوشش آلومينايدي بهوسیله پلاتین
اصولاً آلومیناید های اصلاحشده با پلاتین مقاومت در برابر خوردگی داغ نوع اول را در دو حالت جریان قلیایی یا خنثی برای پوستههای اکسیدی فراهم میکنند. آنها محافظتی اندک را در برابر دماهای پایین خوردگی داغ نوع دوم، که در جریانهای اسیدی اتفاق میافتد، فراهم میکنند. با این حال در برخی از تحقیقات نشان دادند که اگر فاز حاوی پلاتین، در صورتی امکان PtAl2، در فصل مشترک پوشش بانمک پیوسته باشد، این پوشش محافظتی عالی در برابر خوردگی نوع دوم فراهم میکند. هنگامیکه اولين پوششهاي پلاتين آلومينايد يعني LDC-1 ساخته شد، تصور اوليه بر اين بود كه پلاتين در هنگام تشكيل پوشش بهعنوان سدي در برابر نفوذ آلومينيوم عمل میکند ولي مطالعات انجامشده بر روي نحوه توزيع عناصر مختلف در اين پوشش و پوششهاي ديگر مانند RT-22,LDS-2 نشان داد كه پس از عمليات آلومينايزينگ، پلاتين در منطقه خارجي پوشش بهصورت یکلایهPtAl2 بر روي NiAl يا بهصورت ذرات ريز PtAl2 در NiAl باقي میماند. اين نتايج نشان داد كه پلاتين حداقل در برابر نفوذ آلومينيوم به سمت داخل بهعنوان سد عمل میکند.
مطالعات انجامشده بر روي ریزساختار و مكانيزم هاي تشكيل پوشش آلومينايدي پلاتین نشان داده است كه آلومينيوم از ميان پلاتين با سهولت بيشتري نفوذ كرده و لايه اوليه پلاتين بهجای يك سد نفوذي بهصورت يك محيط تسهیلکننده نفوذ آلومينيم به داخل عمل میکند. همچنين نشان داده شده است كه انتقال آلومينيوم از مخلوط پودر پوشش دهي به پوشش در صورت وجود پلاتين در هر دو فرايند LTHA سریعتر انجام میشود. نقش پلاتين در تسهيل نفوذ آلومينيوم در مرحله تشكيل پوشش، در هنگام كاركرد پوشش در دماي بالا نيز گزارششده است.
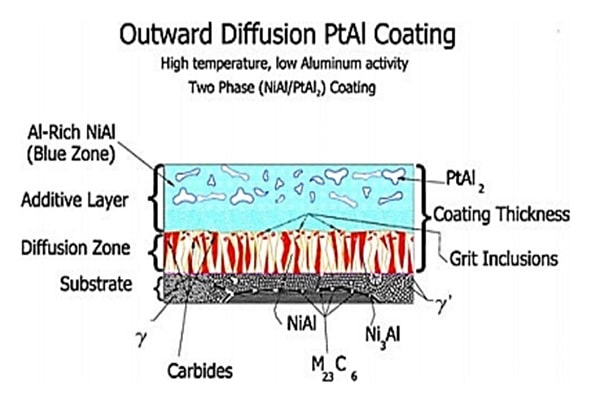
شکل2- 13: طرح واره ریز ساختارپلاتین آلومیناید تشکیل شده با فرآیندLAHT
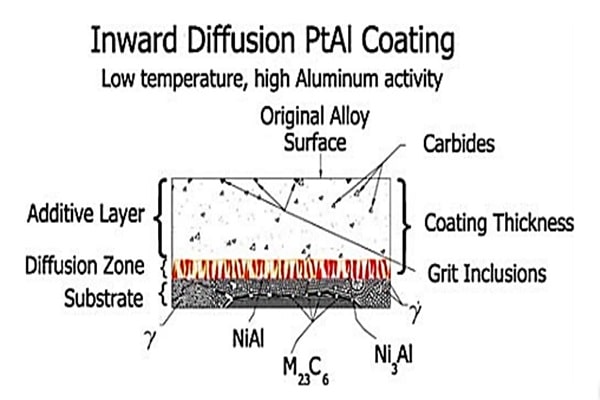
شکل2- 14: طرح واره ریز ساختارپلاتین آلومیناید تشکیل شده با فرآیند HALT
حضور پلاتين در پوشش آلومينايدي باعث افزايش سرعت نفوذ آلومينيوم به سطح میشود، درنتیجه سرعت تشكيل لايه اكسيد آلومينيوم افزایشیافته، یکلایه متراكم Al2O3 بر روي سطح تشكيل میشود و نيز توجيه شده است كه به علت سطح بیقاعده، اكسيد آلومينيوم تشکیلشده بر روي سطح تغليظ شده از پلاتين، چسبندگي بسيار خوبي به پوشش دارد.
كاهش سرعت نفوذ عناصر آلياژي دردمی بالا، سبب افزايش پايداري پوشش میشود. به اين معني كه پلاتين باعث میشود تبديل فاز در زمانهای طولانيتر اتفاق بيافتد البته اين مطلب به اين معني نيست كه پلاتين از نفوذ به سمت خارج نيكل و يا نفوذ به سمت فلز پايه آلومينيم جهت تشكيل فاز NiAl جلوگيري میکند، بلكه با اضافه شدن پلاتين به فاز NiAl يك سيستم تعادلي تشكيل میشود. جدول 2-4 پوشش های نفوذی تجاری اصلاح شده با پلاتین را که توسط شرکت های مختلفی از جمله Howmet، Chromalloy، Turbine component corp و … را نشان می دهد.
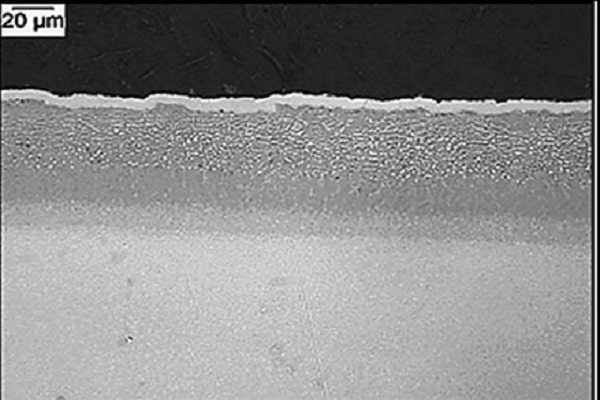
شکل2- 15: تصویر SEM از سطح مقطع پوشش آلومينايدي پلاتین رشد یافته خارجی( لایه سفید فوقانی نیکل است)
جدول2- 4: پوششهای نفوذی تجاری اصلاح شده با پلاتین
نام پوشش | تولید کننده | ترکیب شیمیایی | روش تولید |
LDC 2E | Howmet | پلاتین- آلومیناید | فرآیند محفظه ای با اکتیویته بالا |
MDC 150 | Howmet | پلاتین- آلومیناید | CVD با اکتیویته بالا |
MDC 150L | Howmet | پلاتین- آلومیناید | CVD با اکتیویته پایین |
MDC 151L | Howmet | پلاتین- آلومیناید+Hf,Si,Zr | CVD با اکتیویته پایین |
RT 22 | Chromalloy | پلاتین- آلومیناید | فرآیند محفظه ای با اکتیویته بالا |
RT 44 | Chromalloy | پلاتین-Ru آلومیناید | فرآیند محفظه ای با اکتیویته بالا |
JML 1 | Johnson Matthey | پلاتین- آلومیناید | فرآیند محفظه ای با اکتیویته بالا |
SS 82A | Turbine component corp | پلاتین- آلومیناید | فرآیند بالامحفظه ای با اکتیویته بالا |
SermALcoat | Sermatech | پلاتین- آلومیناید | روکش کاری+ دوغاب+ نفوذ |
اصلاح پوشش آلومینایدی بهوسیله کروم
در سالهای اخیر به پوششهای نفوذی بر پایه غنیسازی سطح با کروم توجه زیادی شده است. کروم دهی در نسل اول و دوم آلیاژهای ریخته با موفقیت محدودی بهکاررفته شده است. ترکیب پوشش کروم براق و با پوشش نفوذی آلومینیم کاربردهای متعدد پیداکرده است. پوششهای نفوذی کروم به خاطر خوردگی داغ کاربردهای محدودی در حفاظت پرههای توربینهای گاز در دماهایی پایینتر از دماهایی که پوشش آلومينايدي کار میکنند، پیداکردهاند.
اضافه كردن كروم به پوشش قبل يا در حين فرايند آلومينايزينگ انجام میشود. براي رسوب كروم میتوان از روشهاي پاششي، سمانتاسيون پودري یا آبکاری قبل از فرآیند سمانتاسيون پودري آلومينيوم يا بهوسیله سمانتاسيون توأم كروم و آلومينيوم استفاده كرد. البته در هر حالت، عمليات حرارتي براي پايدار كردن پوشش و رسيدن به ساختار مطلوب موردنیاز میباشد.
در سال های اخیر، گروه های تحقیقاتی تمرکز گسترده ای در جهت استفاده از افزودنی های مختلف و کاهش دما و زمان سمانتاسیون انجام دادهاند که می توان به تحقیقات ژو و همکارانش اشاره کرد که با کاهش اندازه دانه ذرات و افزودن ایتریا، دمای سمانتاسیون مشترک کروم وآلومینیم را تا ℃800 کاهش داده و به ساختاری کاملا ریزدانه و با کیفیت رسیدند.
با این حال به دلیل اختلاف زیاد در ضریب نفوذ کروم و آلومینیم در لایه β- NiAl، این روش با مشکلاتی مواجه است. جهت رفع این مشکل فرآیند دو مرحله ای توسعه یافته است. در این فرآیند، مراحل کرومایزینگ وآلومینایزینگ به صورت مجزا و به تناوب صورت می گیرد. مثالی از این نوع، پوشش Elcoat-37 تولیدی شرکت البار است. در این روش از کروم، NH4Cl و Al2O3 در دمای ℃950 و زمان 16 ساعت استفاده می شود. نتیجه این عملیات یا سطح غنی از کروم است و یا لایه ترد الفا کروم. اگر پس از این مرحله، آلومینایزینگ با اکتیویته پایین انجام شود لایه خارجی با ساختارβ- NiAl به صورت نفوذ به به خارج تشکیل می شود که در آن کروم در فاز β تا حد اشباع وجود دارد. اگر آلومینایزینگ با اکتیویته بالا انجام شود، پوشش به صورت نفوذ به داخل تشکیل شده و کروم به صورت محلول در فاز β نخواهد بود، بلکه به صورت مناطق غنی از کروم تشکیل می شود.
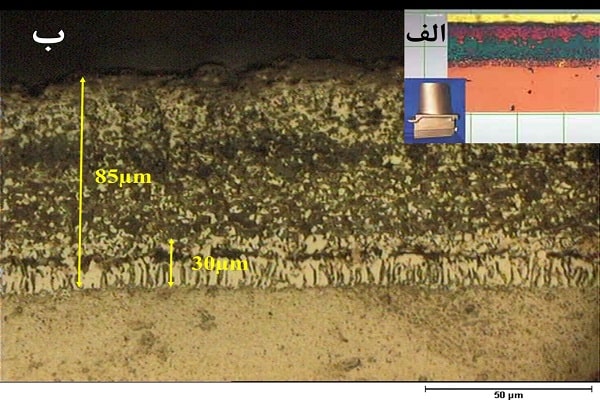
شکل2- 16: تصویر میکروسکوپ نوری پوشش Elcoat37 الف)شرکت هلندیElbar ، ب) شرکت دانش بنیان توربین دوام محافظ
به طور کلی پوشش های نفوذ به داخل حاصل از کرومایزینگ دو مرحله ای خواص بهتری را فراهم می کنند. از نکات منفی این روش می توان به این اشاره کرد که معمولا پوشش حاصل از این روش ناهمگن بوده و دامنه تغییرات ضخامت زیاد است و در صورت برخورد دو نمونه با هم، آن دو نمونه به واسطه نفوذ کروم به هم خواهند چسبید و جدا کردن آنها با از بین بردن پوشش همراه خواهد بود. از جنبه صنعتی، زمان بر بودن پروسه و افزایش قیمت از معایب این روش به شمار می رود. جدول 2-5 تعدادی ازتولید کنندهها و روش تولید پوششهای نفوذی تجاری اصلاح شده با کروم را نشان میهد.
جدول2- 5: پوششهای نفوذی تجاری اصلاح شده با کرو
نام پوشش | تولید کننده | ترکیب شیمیایی | روش تولید |
PWA70-73 | Pratt&Whitny | کروم -آلومیناید | فرآیند محفظه ای با اکتیویته بالا |
MDC 3V | Howmet | کرومایزینگ | فرآیند محفظه ای با اکتیویته بالا |
Snecma C1A | SNECMA | کروماید+ آلومیناید | فرآیند محفظه ای با اکتیویته پایین |
Elcoat 37 | Elbar | کروماید- آلومیناید | فرآیند محفظه ای با اکتیویته پایین |
مکانیزم تاثیر کروم در خوردگی داغ
کلید موفقیت کروم در ممانعت از خوردگی، این است که Cr2O3 را میتوان در چندین حالت ظرفیتی حل کرد که حلالیت آن در مذاب قلیایی به فشار اکسیژن بستگی دارد.
در مذاب اسیدی :
Cr2O3 + 3SO3(Na2SO4) = Cr2(SO4)3
در مذاب قلیایی با اکتیویته اکسیژن پایین:
Cr2O3 + Na3O(Na2SO4) = 2NaCrO2
در مذاب قلیایی با اکتیویته اکسیژن بالا:
2Cr2O3 + 4Na2O(Na2SO4) + 3O2 = 4Na2CrO4
در مذاب قلیایی با اکتیویته اکسیژن بالا:
2Cr2O3 + 2Na2O(Na2SO4) + 3O2 = 2Na2Cr2O7
تمام حالاتی که این واکنشهای به آن منجر میشوند عبارتاند از:
در حضور یک فیلم نازک سولفات، فصل مشترک اسید- سولفات، دارای اکسیژن با اکتیویته پایین میشود. Cr2O3 بهصورت NaCrO2 حل میشود که حلالیت کمتری نسبت به حلالیت Na2CrO4 در فصل مشترک نمک –گازاست.
در فصل مشترک نمک- گاز، اکتیویته اکسیژن بالاتر است، بنابراین Cr2O3 بهصورت Na2CrO4 حل میشود که حلالیت بیشتر بیشتری نسبت به حلالیت NaCrO2 در فصل مشترک اکسید- نمک است.
نتیجه گرادیان حلالیت مثبت است که در فصل مشترک اکسید- نمک کمتر و در فصل مشترک نمک- گاز بیشتر است. گرادیان مثبت انحلال ( در فصل مشترک نمک-گاز) و رسوبگذاری مجدد( در فصل مشترک اکسید- نمک) را پایدار نمیکند، بلکه Cr2O3 تا حد اشباع خود در فصل مشترک اکسید-نمک حل خواهد شد و جلوی انحلال بیشتر را خواهد گرفت.
این سازوکار برای Al2O3 مناسب نیست زیرا فاقد حالات چند ظرفیتی است. گرادیان حلالیت آن نیز منفی است. حل شدن در فصل مشترک اکسید-گاز و رسوبگذاری در فصل مشترک اکسید- نمک از سازوکار تجزیه رسوب ممانعت میکند و پوسته اکسیدی را از بین میبرد. این مدل برای Cr2O3 در یک اسید مذاب نیز بهخوبی پاسخ نمیدهد، زیرا گرادیانی حلالیت منفی دارد که به حل شدن آن در فصل مشترک اکسید-نمک و رسوبگذاری مجدد در فصل مشترک نمک- گاز منجر میشود.
یک مزیت دیگر کروم به آلومینیم این است که Cr2O3 یک اسید در حال رشد با سرعت بیشتراست، بنابراین در شرایطی که پوسته در اثر خوردگی داغ از بین رفته باشد، قادر به تشکیل مجدد زودتر آن خواهد بود.
محدودیت بهکارگیری پوششهای کروم در دماهای بالا (بالای ℃1000)به خاطر قابلیت تبخیر شدن CrO3 حاصل از ترکیب پوسته محافظ Cr2O3 با اکسیژن است. غنیسازی پوشش سوپر آلیاژها پایه نیکل با Cr برای حفاظت در قابل خوردگی داغ موردمطالعه قرارگرفته است.
در پوششهای آلومينايدي افزايش غلظت كروم، خواص حفاظتي پوشش را افزايش میدهد وجود كروم به نحو مؤثری سرعت نفوذ آلومينيم به داخل پوشش را تعديل كرده، مقدار آلومينيم را در حد مطلوب نگه میدارد يعني تبديل فاز به تعويق میافتد كه اين به معناي افزايش عمر پوش میباشد. ميزان انحلال كروم در فازهاي NiAl،Ni3Al در حدود 8% میباشد، درصورتیکه مقدار كروم از اين حد فراتر برود، موجب تشكيل تركيبات بين فلزي بين پوشش و زمينه شده كه تشكيل اين فازها از بهترين عوامل بازدارنده نفوذ آلومينيم از پوشش به داخل فلز پايه يا بالعكس نفوذ نيكل از فلز پايه به پوشش میباشد.
ریز ساختار پوشش کروم- آلومیناید
محققان نشان دادند که ریزساختار پوششهای کروم- آلومیناید از سه لایه، داخلی، میانی و بیرونی تشکیلشده است. شکل 2-17 تصویر میکروسکوپ الکترونی روبشی (SEM) از سطح مقطع پوشش کروم-آلومیناید اعمالی بر روی سوپر آلیاژ پایه نیکلIN738LC را نشان میدهد.
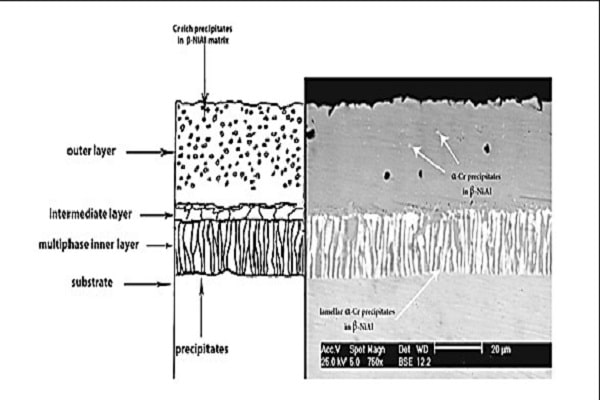
شکل2- 17: تصویر میکروسکوپ الکترونی روبشی (SEM)از سطح مقطع پوشش کروم-آلومیناید اعمالی بر روی سوپر آلیاژ پایه نیکلIN738LC
همانطور که مشاهده میشود این پوشش آلومينايدي از سه لایه اصلی تشکیلشده است:
- لایه داخلی شامل چندلایه از رسوبات غنی از فاز α-Cr در فاز زمینه β- NiAl
- لایه میانی داری فازغنی از β- NiAl همراه با α-Cr
- لایه بیرونی شامل رسوبات فاز α-Cr بهصورت تصادفی درزمینه β- NiAl قرار دارند.
اگر ابتدا بهوسیله كرومايزينگ، كروم بر روي سطح رسوب داده شود یکلایه روغني از كروم بر روي نمونه ايجاد میشود و سپس اين لايه به يك كروم α كه تردي بسيار بالايي دارد تبديل میشود. انجام آلومينايزينگ در دماي بالا و فعاليت پايين باعث میشود كروم در لايه خارجي فقط در محدوده انحلال فاز NiAl-β وجود داشته باشد و بيشترين غلظت كروم در قسمتهای داخلي پوشش تجمع میکنند و در صورت انجام عمليات آلومينايزينگ در دماي پايين و فعاليت بالا به علت رشد جهتدار پوشش كروم بهصورت فازهاي غني از كروم به شكل پراكنده در لايه خارجي پوشش باقي میماند. لذا به علت توزيع بهتر كاربيدها در حالت آلومينايزينگ با فعاليت پايين، كيفيت پوشش كروم – آلومينايد مطلوبتر است.
اکسیداسیون پوشش کروم- آلومیناید
گوودلیوسکا با بررسی اثر فعالکنندههای هالیدی(NaF-NH4Cl-CrF2-Na3AlF6) در پوششهای کروم –آلومیناید و آلومیناید نشان داد که هالید NH4Cl به دلیل فشار بخاربالاتر نسبت به هالیدهای متناظر، بهترین اثر پذیری را در انتقال کروم به سطح پوشش در پوشش های کرومایزینگ دارد. همچنین نشان دادن که غلظت کروم در بر روی سطح پوشش در حضور آمونیوم کلراید در فرآیند کرومایزینگ حدود 40 درصد است که تقریبا برابر مقدار حلالیت کروم در نیکل است این درحالی است غاظت کروم در استفاده از فعال کنندههای فلوریید ها پس از فرايند کرومایزینگ کمتر از 20 درصد بوده و باعث ایجاد فاز نامطوب کروم می شود که از تردی بالایی برخوردار است. طبق تحقیقات انجام شده در مود اثرپذیری هالیدها در مورد پوشش آلومینایزینگ مشاهده شد که هالیدها در انتقال آلومینیم تاثیر چندانی نداشته و بیشتر به فعالیت آلومینیم در ترکیب بستگی دارد.
در یک پژوهش سوپرآلیاژ پایه نیکل اینکونل 600 با دو نوع پوشش کرمایزینگ –آلومینایزینگ و کرومایزینگ –ایتریم – آلومینایزینگ پوشش داده شد. فرآیند پوشش در دمای 1050 به مدت 8 ساعت اعمال شد. و از نظر اکسیداسیون با هم مقایسه شدند.نتایج نشان داد که افزودن کروم وایتریم باعث افزایش مقاومت به اکسیداسیون می شود . اکسیداسیون سیکلی برای دو نوع پوشش در دمای 700-1100 درجه سانتی گراد با زمان 10 ساعت برای هر سیکل انجام شد.نتایج نشان داد که پوشش ایتریم کروم الومیناید اصلاح شده مقاومت اکسیداسیون بهتری نسبت به پوشش کروم الومیناد نشان داد. نقش ایتریم را به بهبود چسبندگی لایه اکسیدی نسبت داد.
یانگ و همکارن با بررسی رفتار اکسیداسیون پوشش آلومينايدي و پوشش های آلومینادی اصلاح شده با کروم و سیلسیسم در دمای 1100 درجه سانتی گراد بر روی آلیاژ IC20 نشان دادن که افزودن سیلیسیم باعث افزایش مقاومت به اکسیداسیون نسبت به پوشش های آلومینایدی ساده و نمونه آلیاژ بدون پوشش می شود. همچنین با افزودن کروم به پوشش سیلیسیم آلومیناید به نحو موثري سرعت نفوذ آلومينيم به داخل پوشش را تعديل كرده، مقدار آلومينيم را در حد مطلوب نگه مي داردو باعث چسبندگی بیشتر پوشش می شود يعني تبديل فاز به تعويق مي افتد كه اين به معناي افزايش عمر پوش مي باشد.
دولابی و همکاران رفتار اکسیداسیون سیکلی و هم دمای پوشش های کروم –آلومیناید را مورد بررسی قرار دادند. برای اعمال پوشش کروم –آلومیناید از روش سمانتاسیون پودری دو مرحله ای بر روی سوپرالیاژ پایه نیکل IN738 استفاده شد. در مرحله اول پوشش کرومایزینگ را در دمای ℃1100 به مدت 5 ساعت انجام شددر مرحله دوم پوشش آلومینایزیگ در دمای ℃750 و به مدت ساعت انجام شد و سپس عملیات حرارتی شدند. برای بررس رفتار اکسیداسیون پوششها از دو روش اکسیداسیون سیکلی و همدما استفاده شد. دمای اکسیداسیون 900 درجه و زمان هر سیکل 25 ساعت برای هر دو روش در نظر گرفته شد با این تفاوت که در اکسیداسیون همدما نمونه ها در داخل کوره سرد شدند ولی برای اکسیداسیون سیکلی پس از هر سیکل نمونه ها به مدت 30 دقیقه به وسیله فن سریع سرد شدند.
نتایج اکسیداسیون نشان داد حمله اکسیژن برای اکسیداسیون سیکلی نسبت به اکسیداسیون همدما شدیدتر بوده به طوری که نمونههای اکسیداسیون سیکلی پس از 350 ساعت تخریب و نمونه های اکسیداسیون همدما پس از 700 ساعت تخریب شدند. سینیتیک واکنشها نشان داد که اکسیداسیون هم دما از قانون پارابولیک پیروی می کند در حالی که اکسیداسیون سیکلی در درجه اول( سیکل 12) مشابه قانون پارابولیک بوده ودر نهایت سطح شدیتر مورد تخریب قرار گرفته است. با بررسی اندازه دانه نمونه درزمان 350 ساعت و 700 ساعت برای اکسیداسیون هم دما مشاهده شد که اندازه دانه با افزایش زمان از 206 میکرون به 4.4 میکرون افزایش پیدا کرده است.
در یک پژوهش پس از مشخصه یابی پوشش های تجاری Elcoat 101 وElcoat 37 ، مقاومت به اکسیداسیون چرخهای آنها در دو دمای ℃850 و ℃1050 مورد بررسی قرار گرفت. بدین منظور نمونههای سوپرآلیاژ پایه نیکل پوشش دار برای آزمون اکسیداسیون سیکلی، در سیکل های 5 ساعته در اتمسفر کوره آزمایش شدند. کنتیک فرآیند ها توسط منحنی تغییر وزن بر اساس زمان بررسی شد. نتایج بررسی پوشش های تجاری نشان داد که اکسیداسیون سیکلی هر دو پوشش آلومينايدي از قانون سهمی پیروی می کند و ثابت سهمی در حدود 1000 برابر کمتر از ثابت سهمی سوپرآلیاژ بدون پوشش است. پوشش Elcoat 101 در برابر اکسیداسیون سیکلی مقاومت بیشتری از خود نشان داد. مورفولوژی محصولات اکسیداسیون هر دو پوشش در دمای ℃850 سوزنی شکل و در دمای ℃1050کروی شکل بود محققان این امر را ناشی از حضور کروم در ترکیب شیمیایی اکسید در دمای بالا می دانند.
مشاوره خرید مواد شیمیایی با کارشناسان اَوِسیناشیمی
شما عزیزان می توانید برای کسب اطلاعات بیشتر راجع به مواد شیمیایی و همچنین استعلام قیمت و موجودی با کارشناسان مجموعه اَوِسینا شیمی تماس بگیرید و یا از طریق شبکه های اجتماعی پیام دهید تا در سریع ترین زمان ممکن با شما تماس بگیریم.